CFD Analysis of NACA 2412 Airfoil
Background
The NACA 2412 airfoil, a widely studied and utilized airfoil in aerodynamics, is known for its stable performance across various applications. This project focuses on evaluating how geometric deformations impact its lift and drag characteristics, crucial for maintaining optimal efficiency in aerospace applications.
Project Overview
Performed Computational Fluid Dynamics (CFD) analysis on a NACA 2412 airfoil to evaluate its aerodynamic performance under deformation and varying angles of attack. The airfoil data file was sourced from Airfoil Tools.
CFD is a powerful tool that numerically solves fluid dynamics equations to analyze flow behavior and aerodynamic performance. It allows engineers to evaluate designs under various conditions without expensive wind tunnel testing.
Problem Statement
Surface smoothness significantly influences aerodynamic performance. Deformations, even minor, can disrupt airflow, leading to increased drag and reduced lift. This study aims to evaluate the extent of these effects using CFD simulations and highlight the importance of maintaining airfoil integrity in design and manufacturing.
Methodology
- Created a 2D model of the NACA 2412 airfoil in ANSYS Fluent.
- Simulated airflow at angles of attack ranging from -5° to 10°.
- Introduced geometric deformations (peg protrusions) to analyze their effects on lift and drag coefficients.
- Applied boundary conditions: inlet velocity, outlet pressure, and no-slip walls.
- Used mesh refinement near the airfoil surface to capture detailed flow phenomena.
- Implemented k-ω turbulence models for transitional flow analysis.
Analysis and Results
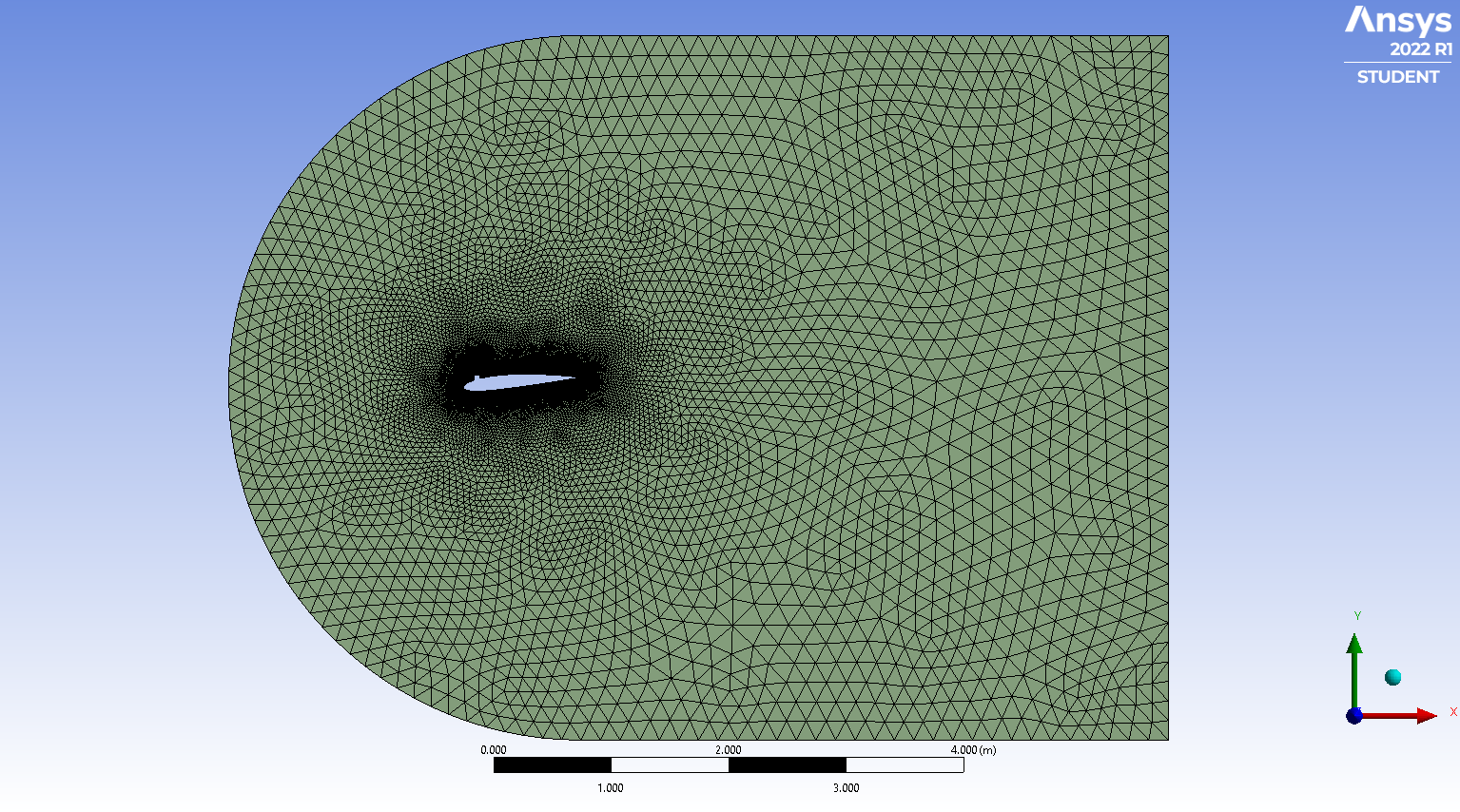
Figure 1: Mesh configuration of the NACA 2412 airfoil
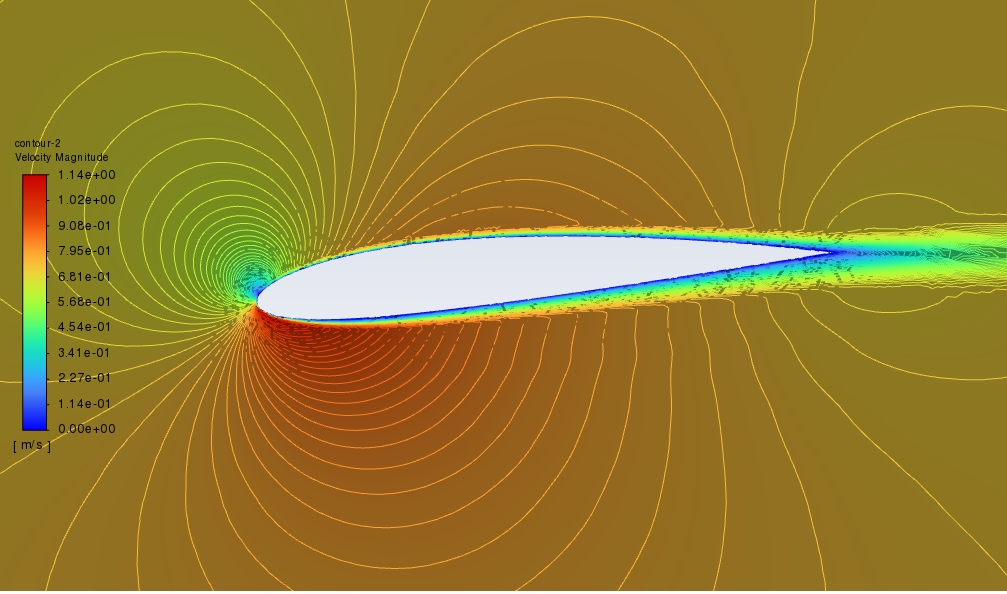
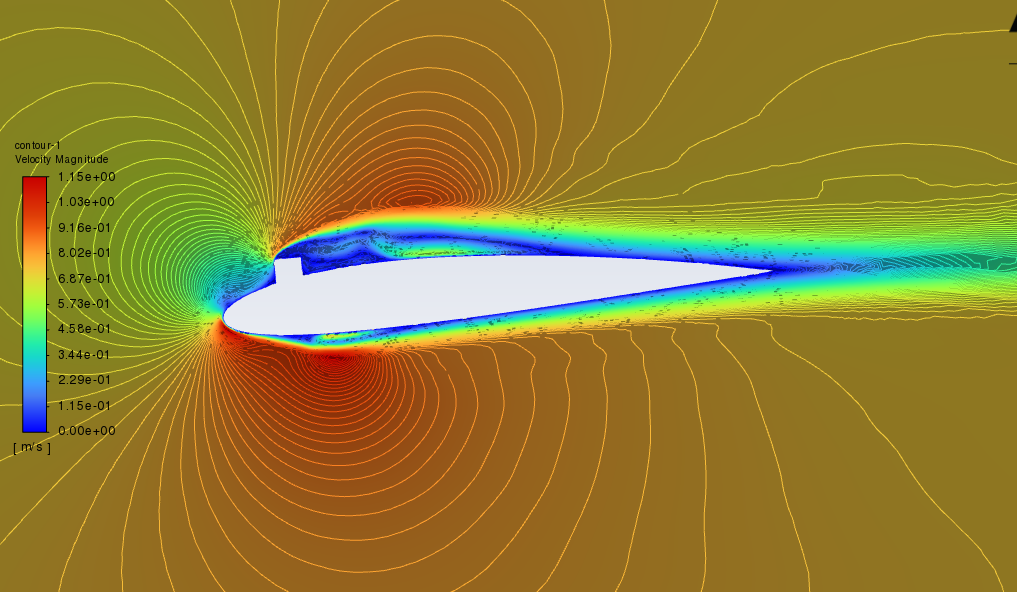
Figure 2: Velocity profile comparison (left: no deformation, right: with deformation)
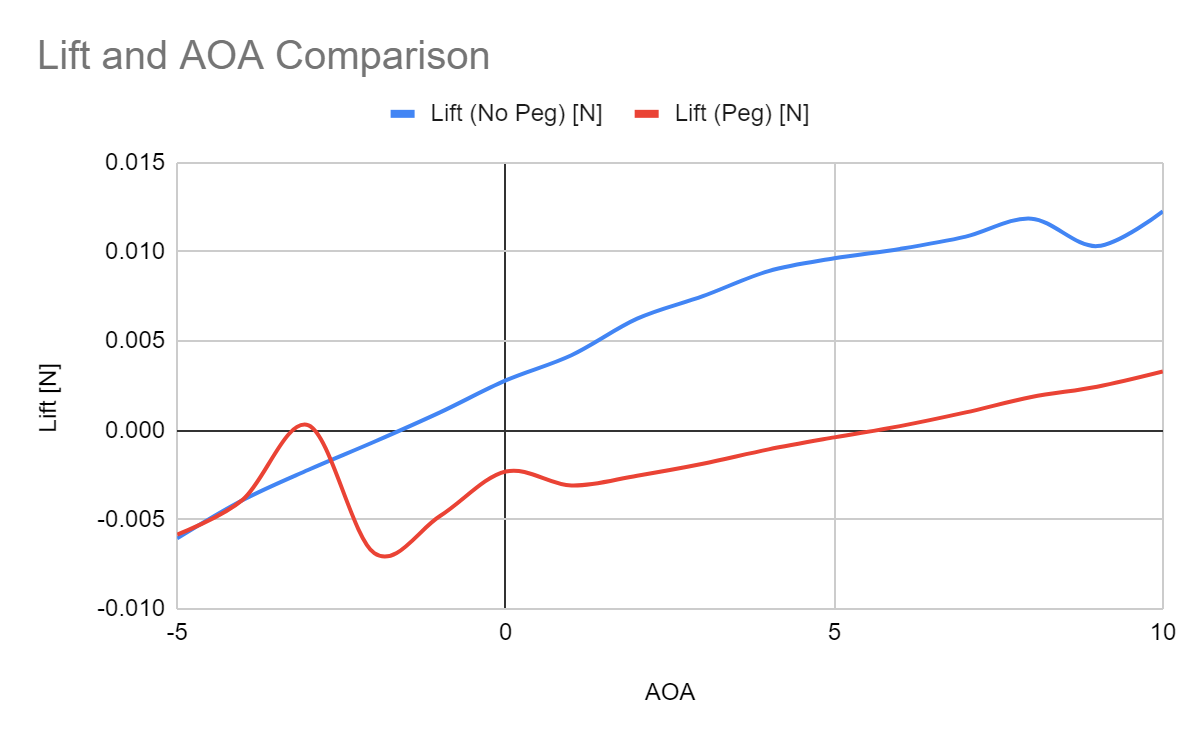
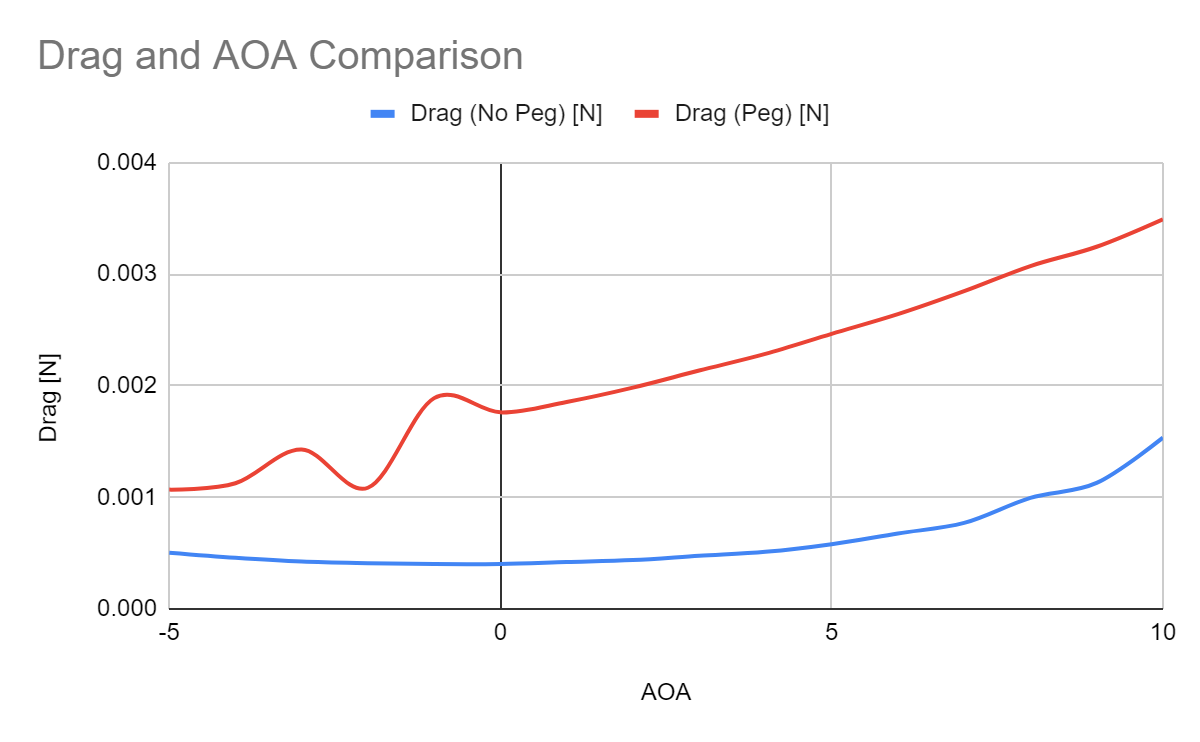
Figure 3: Comparison of lift and drag vs. angle of attack
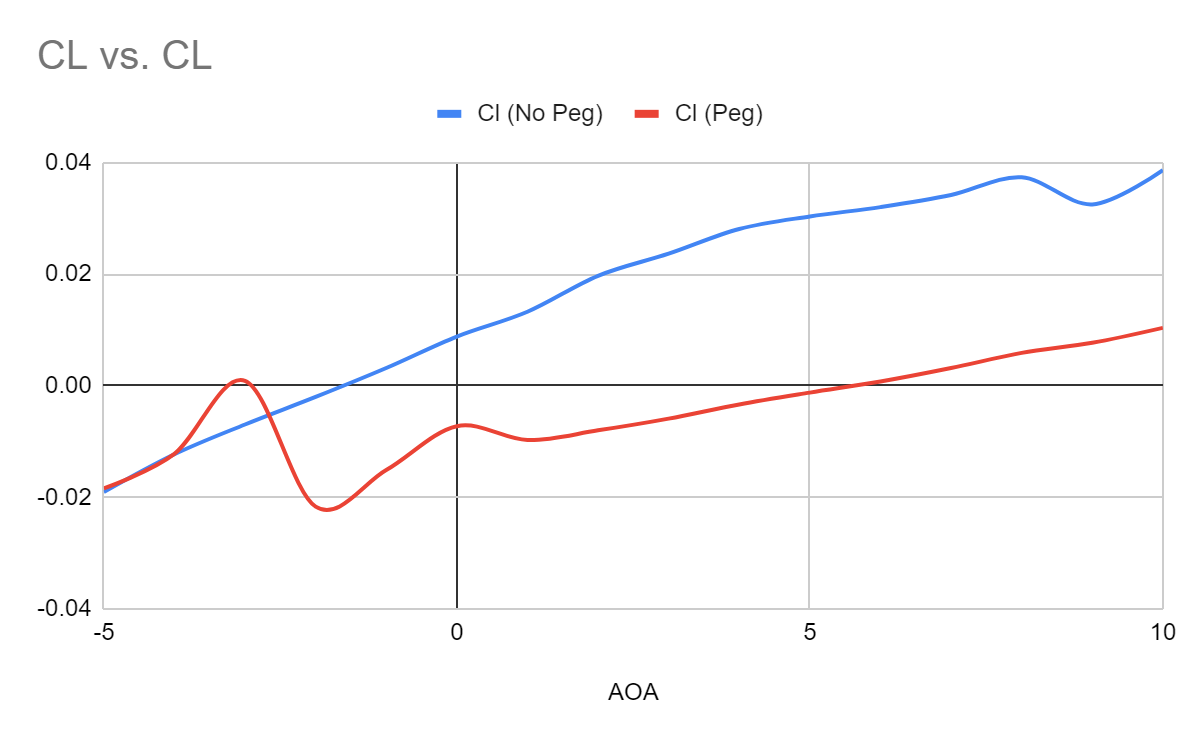
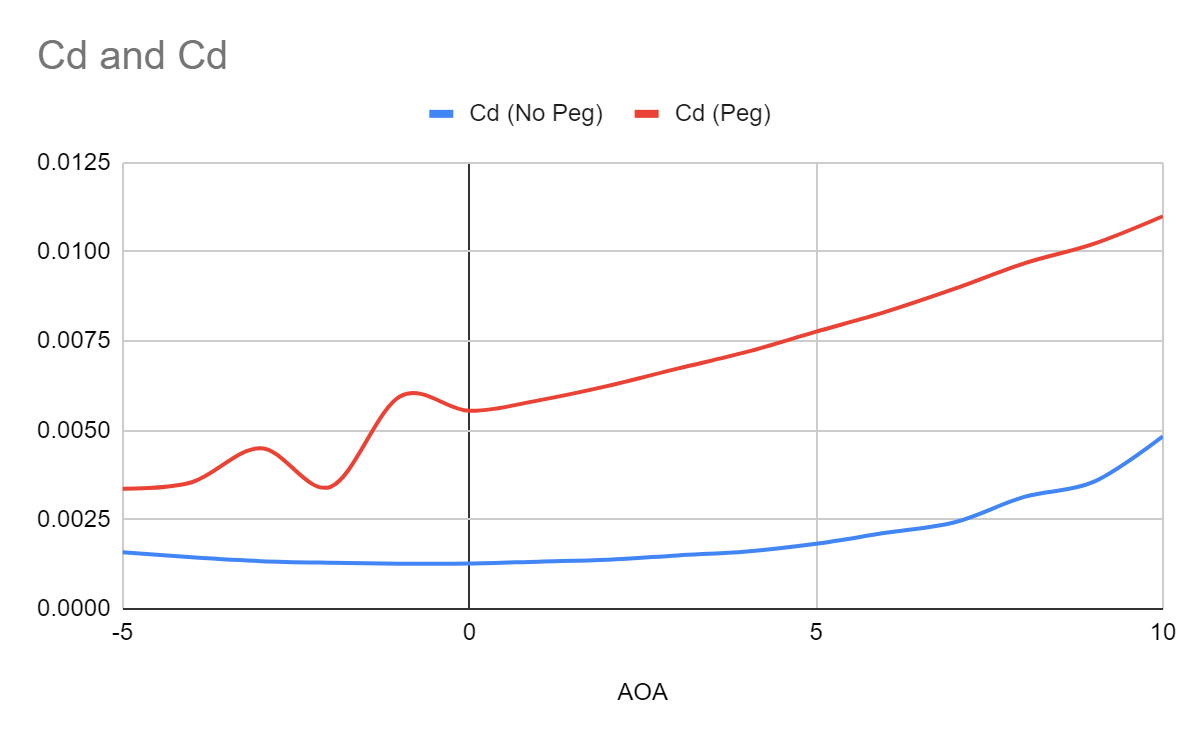
Figure 4: Lift (Cl) and Drag (Cd) coefficient comparisons (left: Cl, right: Cd)
Impact and Business Relevance
This project demonstrates the critical role of airfoil surface smoothness in optimizing aerodynamic performance. The findings provide actionable insights for industries such as aerospace, automotive, and renewable energy:
- Cost Reduction: Identifying and addressing surface imperfections during manufacturing can prevent costly inefficiencies, such as increased fuel consumption due to higher drag.
- Performance Optimization: Improved design strategies based on the findings can enhance lift-to-drag ratios, allowing for lighter and more efficient structures.
- Sustainability: Enhanced aerodynamic efficiency leads to reduced emissions, aligning with green energy goals and compliance with environmental regulations.
- Proactive Maintenance: Regular inspections and corrective actions to address deformation can extend the lifespan and reliability of airfoils in operation.
Conclusion
The CFD analysis highlighted the sensitivity of lift and drag performance to geometric deformations, emphasizing the need for precision in airfoil manufacturing. By maintaining smooth airfoil surfaces, industries can achieve better performance, lower operational costs, and contribute to sustainability goals. This study reinforces the importance of using advanced computational tools to predict and mitigate aerodynamic losses effectively.
Tools and Skills Used
- ANSYS Fluent
- Geometric Modeling
- Flow Simulation and Analysis
- Aerodynamic Coefficient Calculation
Learn More
If you’re interested in diving deeper into this project, feel free to explore the following resources: