Thermodynamic Properties and Nozzle Performance: Insights and Applications
Project Overview
When designing engineering systems—whether for space exploration or industrial applications—the choice of the working fluid is critical. This decision directly impacts efficiency, cost, and practicality. Two contrasting examples highlight the importance of selecting the right gas:
- NASA’s Space Shuttle: Used liquid hydrogen (H₂) with liquid oxygen (LOX) for propulsion. Achieved high efficiency due to hydrogen's superior energy-to-mass ratio, but faced challenges with cryogenic storage needs and high costs.
- SpaceX’s Starship: Employs methane (CH₄) and LOX in its Raptor engines. Balances efficiency with easier storage and potential in-situ production on Mars, aligning with long-term colonization goals.
Thermodynamic Properties of Gases
The first phase of this project analyzed six gases—air, nitrogen, steam, methane, helium, and hydrogen—focusing on their thermodynamic properties and suitability for various applications. These properties, including the gas constant (R), specific heat ratios (γ), and speed of sound, play pivotal roles in determining energy efficiency and flow dynamics.
Key Findings:
- Hydrogen (H₂): Exceptional energy-to-mass ratio and the highest speed of sound trend, ideal for high-speed flows. However, it demands cryogenic storage and poses safety concerns.
- Methane (CH₄): Strikes a balance between efficiency and practical handling, making it a preferred choice for propulsion and energy systems.
- Air and Nitrogen (N₂): Baseline gases with well-understood properties, suitable for testing and industrial applications.
To compare the thermodynamic properties of the gases, we utilized the speed of sound formula as a key metric:
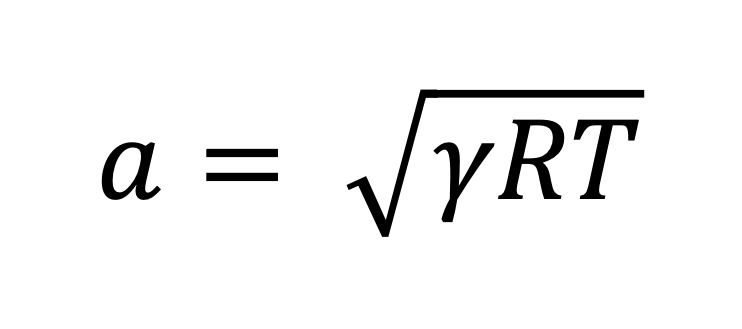
Where:
a
: Speed of sound (m/s)\gamma
: Specific heat ratio (dimensionless)R
: Gas constant (J/kg·K)T
: Absolute temperature (K)
This formula links the thermodynamic properties of the gas—such as its ability to transfer energy and resist compression—with its practical applications in high-speed flows and nozzle performance. By calculating and comparing the speed of sound for each gas over a range of temperatures, we gained insights into their suitability for specific engineering applications.
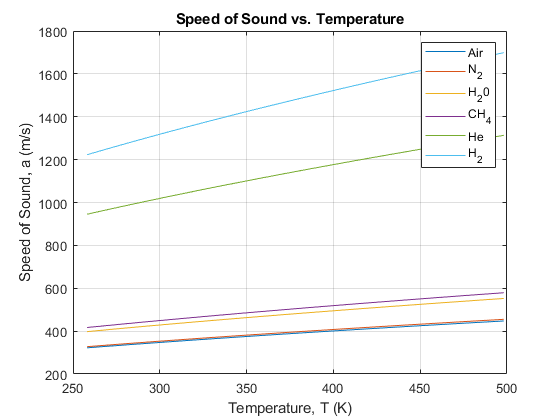
Figure: Speed of Sound vs. Temperature
Thermodynamic Properties Table:
Ideal Gas | Gas Constant (R) (kJ/kg·K) | Specific Heat, Cp (kJ/kg·K) | Specific Heat, Cv (kJ/kg·K) | Specific Heat Ratio (γ) |
---|---|---|---|---|
Air | 0.2870 | 1.005 | 0.718 | 1.400 |
Nitrogen (N₂) | 0.2968 | 1.039 | 0.743 | 1.400 |
Steam (H₂O) | 0.4615 | 1.8723 | 1.4108 | 1.327 |
Methane (CH₄) | 0.5182 | 2.2537 | 1.7354 | 1.299 |
Helium (He) | 2.0769 | 5.1926 | 3.1156 | 1.667 |
Hydrogen (H₂) | 4.1240 | 14.307 | 10.183 | 1.405 |
Nozzle Performance Analysis
Nozzles are essential in systems ranging from rocket engines to industrial turbines. They convert high-pressure, high-temperature gases into high-velocity outputs, optimizing energy transfer and thrust.
The findings for mass flow rate were derived by substituting key thermodynamic parameters into the dimensionless mass flow rate equation. This process involved aligning assumptions about isentropic flow and efficiency to simplify the equations for practical scenarios, revealing critical relationships between Mach number, flow velocity, and pressure changes.
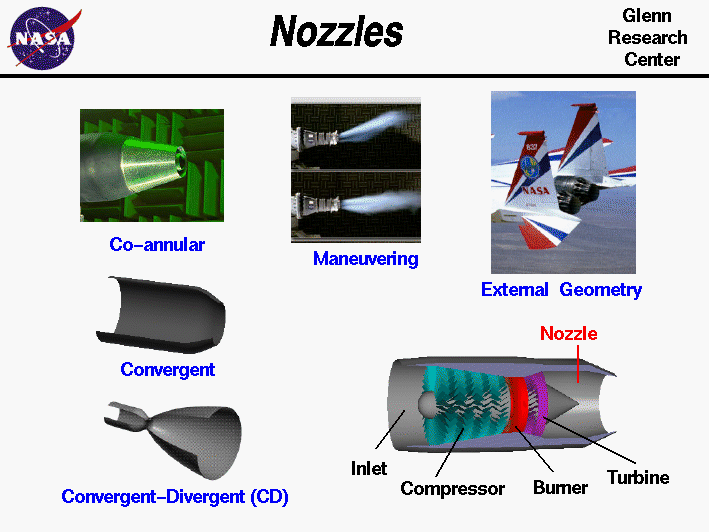
Figure: Nozzle design (Image credit: NASA)
Key Assumptions:
- Isentropic Flow: Initial calculations assumed frictionless, ideal flow.
- Steady-State Conditions: Ignored transient effects and assumed consistent flow.
- One-Dimensional Flow: Simplified analysis by neglecting variations across the nozzle's cross-section.
- Constant Specific Heat Ratio (γ): Assumed γ was temperature-independent.
Results and Insights:
- Efficiency vs. Mass Flow Rate:
- For η=0.98: Dimensionless mass flow rate = 0.570
- For η=0.99: Dimensionless mass flow rate = 0.575
- For η=1.00: Dimensionless mass flow rate = 0.579 (theoretical maximum)
- Impact of Mach Number: As M approaches or exceeds 1 (sonic to supersonic flow), nozzle performance changes dramatically, highlighting the importance of precise design.
Real-World Applications
- Aerospace Engineering: Rockets can maximize thrust and fuel efficiency by leveraging hydrogen’s properties and optimizing nozzle design.
- Clean Energy: Hydrogen-powered systems and fuel cells benefit from reduced losses in nozzles.
- Industrial Turbines: Improved nozzle designs save energy and lower operational costs.
Why It Matters
This project demonstrated that small design changes can lead to significant improvements in system efficiency, cost-effectiveness, and adaptability. Understanding gas properties and nozzle performance equips engineers with tools to innovate and meet both current and future challenges in aerospace, energy, and industrial systems.
Learn More
If you’re interested in diving deeper into this project, feel free to explore the following resources: