Turbojet vs. Turbofan Engine Performance Analysis
Project Overview
The project explores the comparison of turbojet and turbofan engines, focusing on their efficiency, thrust-specific fuel consumption (TSFC), and performance across various flight conditions. Turbojets and turbofans represent the two primary engine configurations in modern aviation, each suited for distinct applications. This study utilizes Parametric Cycle Analysis (PCA) to evaluate and optimize engine performance under varying Mach numbers, compressor pressure ratios, and fuel properties.
Turbojets are optimized for high-speed supersonic applications, while turbofans excel in subsonic regimes with higher bypass ratios for greater fuel efficiency. PCA provides a comprehensive framework to analyze these differences, making it a critical tool in propulsion system design and operation.
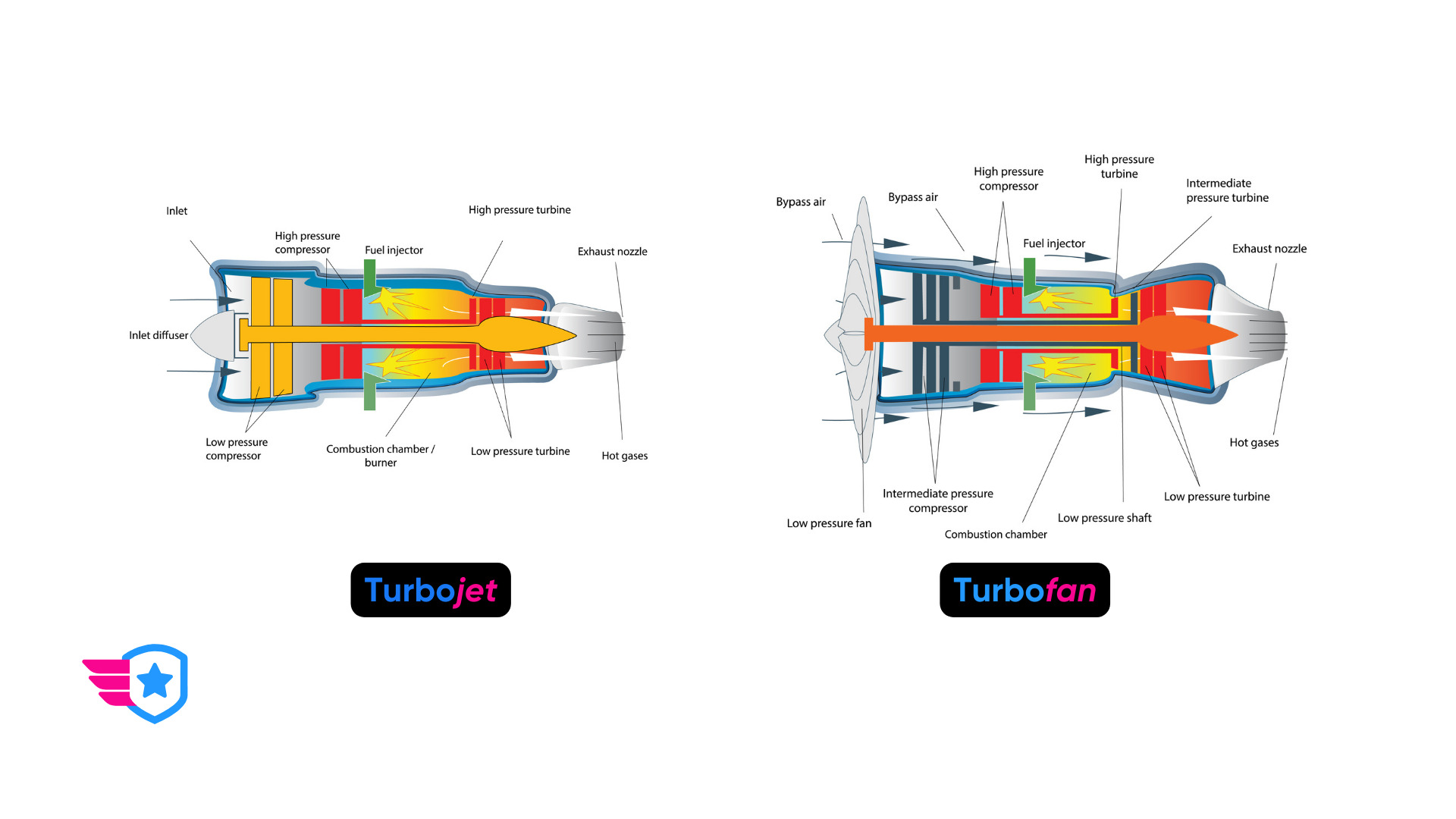
Figure: Turbojet vs. Turbofan Comparison (Image Credit: Pilot Institute)
Problem Statement
Determining the optimal engine type for specific flight conditions involves addressing complex trade-offs between efficiency, thrust, and operational costs. Turbojets and turbofans, while sharing similar thermodynamic principles, vary significantly in their design and applications. This project aims to identify these differences and evaluate their impact on overall engine performance using PCA.
Methodology
- Conducted Parametric Cycle Analysis (PCA) to model engine performance under varying conditions.
- Simulated performance metrics, including TSFC and thermal efficiency, at Mach numbers ranging from 0.5 to 3.0.
- Plotted 3D graphs comparing the effects of compressor pressure ratios and heating power on engine efficiency.
- Normalized data for turbofans with different bypass ratios to highlight comparative performance trends.
Background Information
Turbojet Engines: Designed for high-speed applications, turbojets generate thrust by expelling exhaust gases at high velocities. They are ideal for supersonic aircraft but exhibit lower fuel efficiency and higher noise levels in subsonic conditions.
Turbofan Engines: Incorporating a large fan to bypass air, turbofans offer improved fuel efficiency and reduced noise, making them the engine of choice for commercial aviation. Their higher bypass ratios contribute to better propulsive efficiency in subsonic flight.
Parametric Cycle Analysis (PCA): PCA is a critical tool for evaluating the performance of turbine engines. It analyzes relationships between parameters like Mach number, temperature ratios, and compressor pressure ratios to optimize engine design and operation. This approach ensures engines meet performance requirements while minimizing operational costs.
Analysis and Results
- Turbofans demonstrated 20% higher efficiency in subsonic conditions due to their high bypass ratio.
- Turbojets excelled at speeds above Mach 2.5, showcasing their superiority in high-speed applications.
- Compressor pressure ratio improvements led to a 20% gain in thermal efficiency for both engine types.
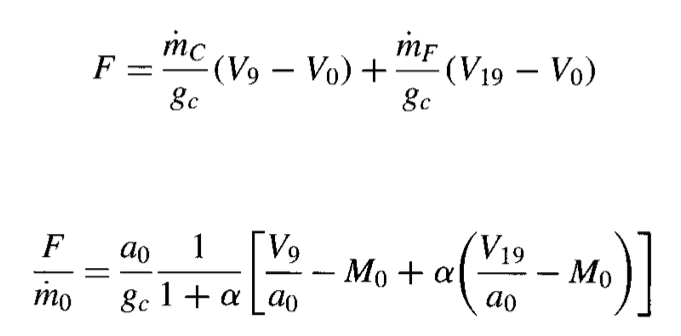
Figure: Thrust of the Ideal Turbofan Engine
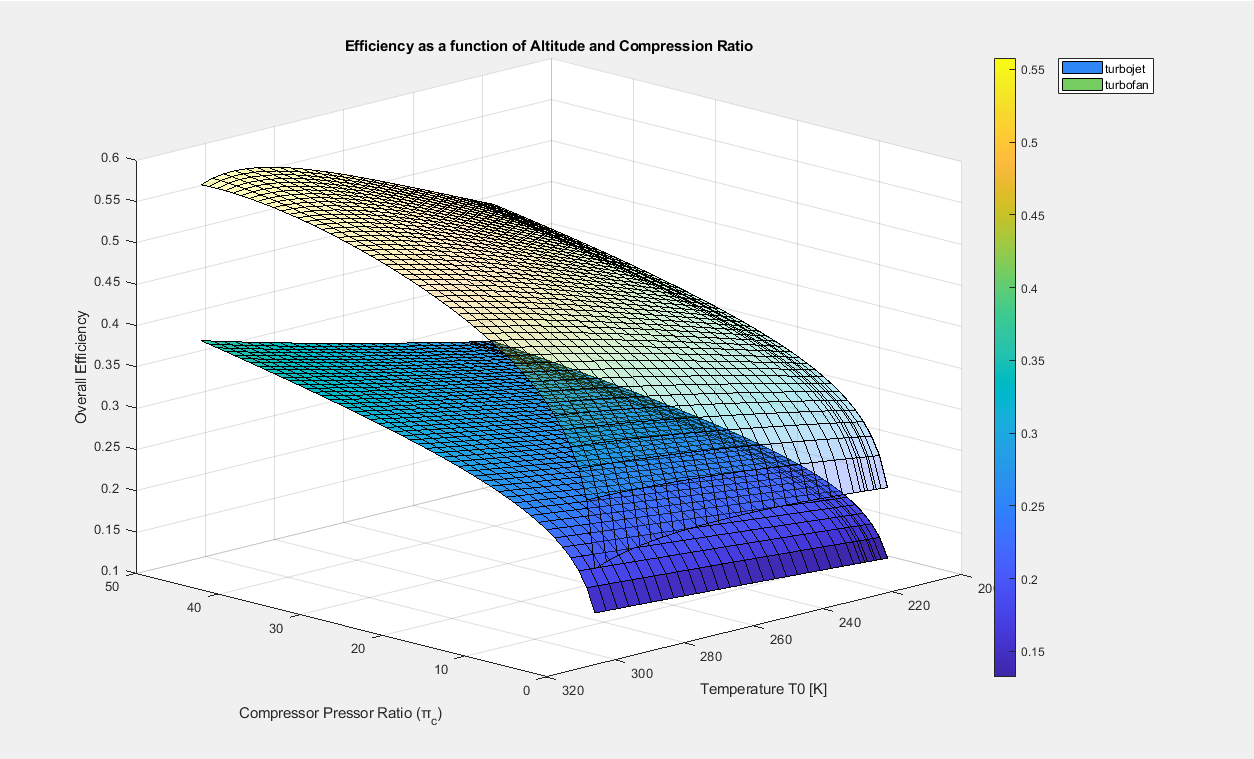
Figure 1: Ideal Turbojet and Turbofan Overall Efficiency as a Function of Altitude and Compression Ratio
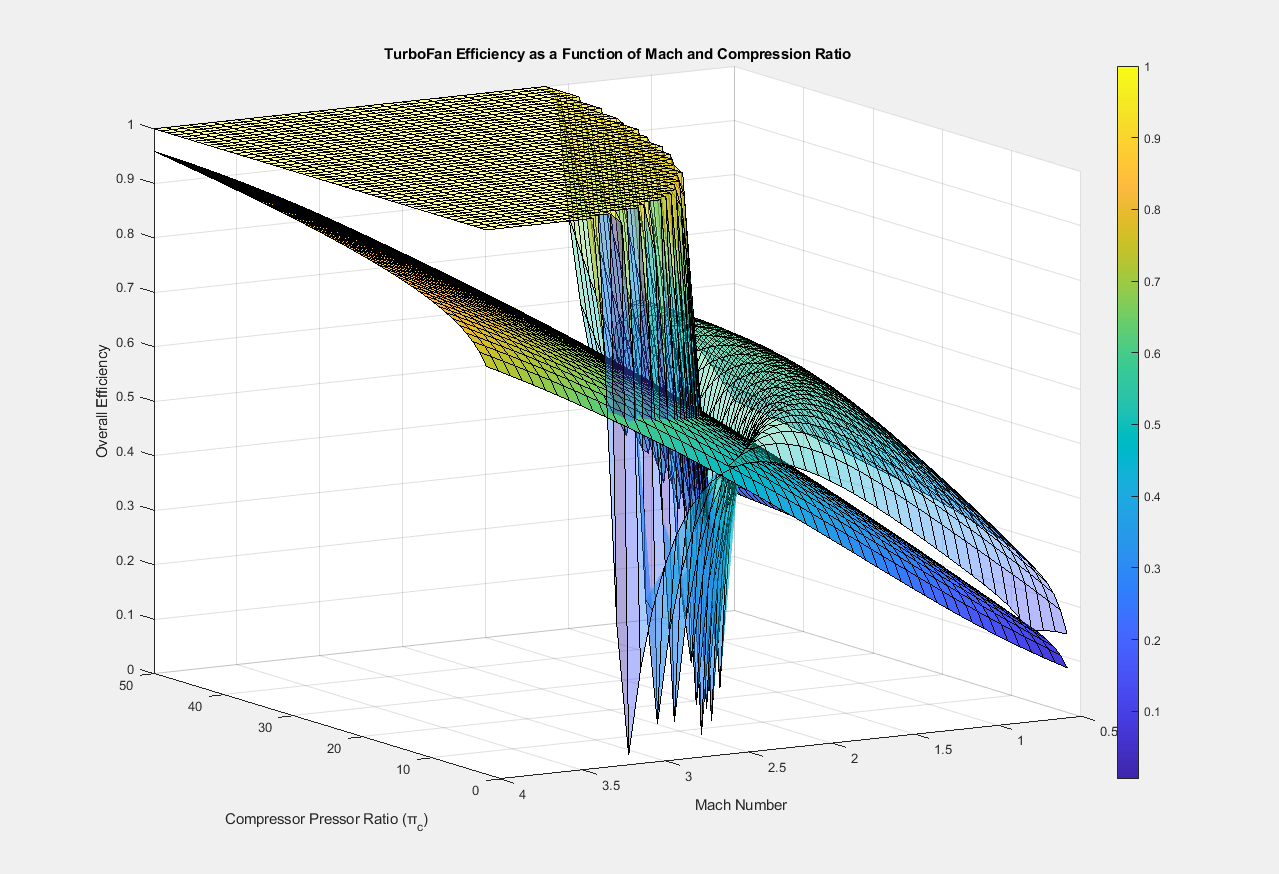
Figure 2: Ideal Turbojet and Turbofan Overall Efficiency as a Function of Compression Ratio and Mach Number
Conclusion
The analysis underscores the strengths of turbofans in subsonic applications due to superior fuel efficiency and lower operational costs. Conversely, turbojets provide unmatched performance in supersonic regimes, making them ideal for specialized missions. Parametric Cycle Analysis (PCA) proved instrumental in deriving these insights, highlighting its value in propulsion system optimization.
Understanding these trade-offs is critical for designing engines that match the performance needs of specific applications. By leveraging PCA, engineers can make informed decisions that lead to more efficient, cost-effective propulsion systems. This not only benefits the aviation industry through reduced operational expenses but also contributes to environmental sustainability by optimizing fuel consumption and minimizing emissions.
The importance of PCA extends to shaping future advancements in hybrid engine designs, such as adaptive cycle engines, which aim to combine the benefits of both turbojets and turbofans. Furthermore, PCA provides a robust framework for addressing operational challenges and ensuring propulsion systems are tailored to meet the rigorous demands of modern and future aviation.
Tools and Skills Used
- MATLAB Simulations
- Parametric Cycle Analysis
- Thermal Efficiency and TSFC Calculations
- Comparative Performance Modeling
Learn More
If you’re interested in diving deeper into this project, feel free to explore the following resources: