The Shear Center: A Structural Balancing Act
Project Overview
The shear center is a critical point in the cross-section of a structural member where an applied load does not induce torsion. This laboratory experiment aimed to empirically determine the shear center of a channel-shaped beam by applying various loads and comparing experimental results to theoretical predictions. The results demonstrated significant deviations, highlighting the challenges of manual measurements and the potential for computational tools to enhance precision.
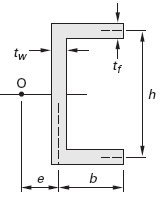
Figure: Channel Shaped Beam where e is the distance to the shear center
Introduction
Every structure, from skyscrapers to aircraft wings, must contend with the forces acting upon them. Among these forces, torsion poses a unique challenge, as it can twist and weaken beams if loads are not aligned with the shear center.
The shear center represents the balance point where applied loads induce bending without twisting. For engineers, locating the shear center is not just theoretical—it directly impacts the safety, stability, and efficiency of structures ranging from bridges to fuselages.
This experiment sought to locate the shear center of a channel-shaped beam, a common yet asymmetrical structural element prone to torsion. By combining manual measurements with strain gauge data, the study provided a hands-on approach to understanding how theoretical concepts manifest in real-world scenarios.
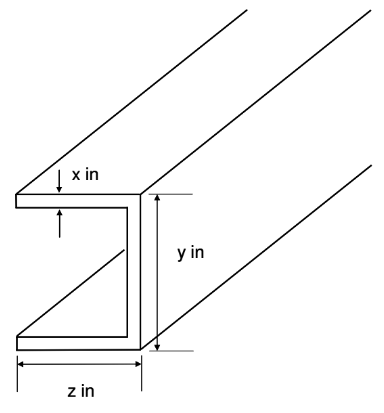
Figure 1: Channel Beam Sketch
Experimental Setup
The experiment was conducted using a channel-shaped cantilever beam equipped with a three-channel strain gauge. The setup included:
- The Beam: A channel-shaped cross-section with an asymmetrical open design, making it prone to twisting when loads are misaligned.
- Strain Gauge:
- Channel 1 (X-axis): Measured torsion. The goal was to reduce this reading to zero, indicating no twisting.
- Channel 2 (Y-axis): Measured pure bending forces.
- Channel 3 (Z-axis): Captured moments resulting from the applied load.
- The Flanged Pipe: A horizontal pipe mounted on the beam served as the load application mechanism. Weights could be hung and adjusted to achieve equilibrium.
- Loads: Three different masses (2395 g, 4595 g, 6795 g) were applied incrementally, with their positions adjusted until the strain gauge readings indicated zero torsion on Channel 1.
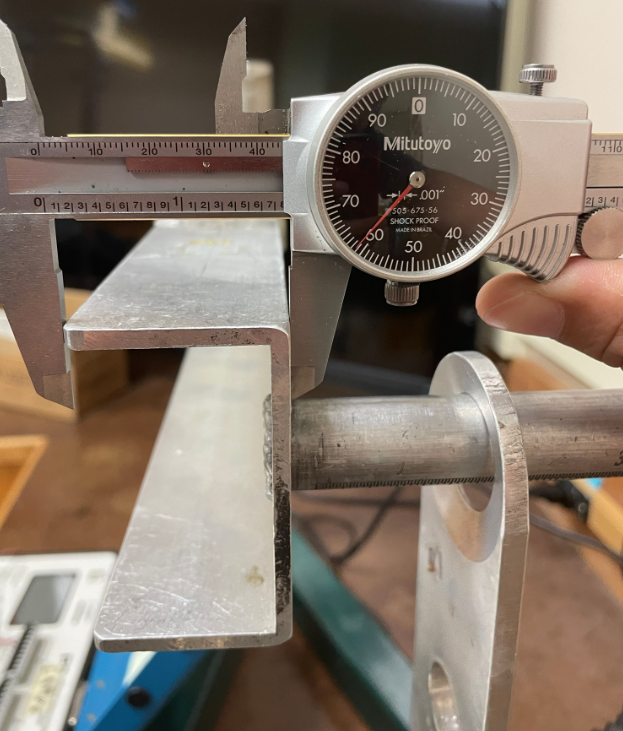
Figure 2: Flanged Pipe with Weight Setup
Results
Empirical data was collected for each load, and the strain readings were tabulated:
Load (g) | CH1 μ (X-axis) | CH2 μ (Y-axis) | CH3 μ (Z-axis) | Distance (in) |
---|---|---|---|---|
2395 | 0 | 13 | -394 | 1.375 |
4595 | 0 | 24 | -388 | 1.255 |
6795 | 0 | 35 | -381 | 1.185 |
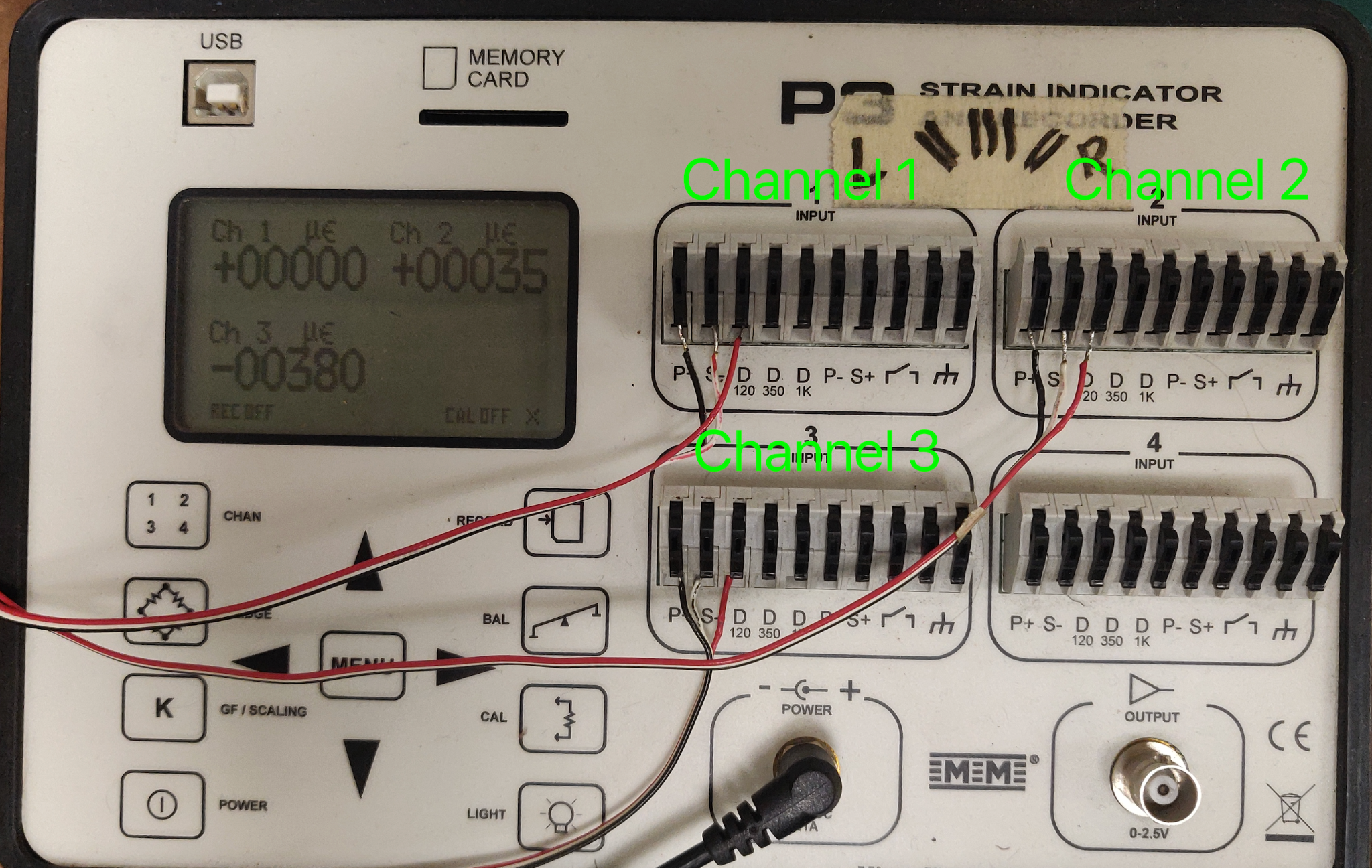
Figure: Strain Gauge Indicator with Three Channels
Discussion
The experimental data highlighted several key challenges:
- Flanged Pipe Alignment: Minor misalignments in load positioning could have contributed to deviations.
- Measurement Precision: Slight variations in positioning or strain gauge readings affected the results.
- Beam Imperfections: Real-world material inconsistencies played a role in the discrepancies.
- Simplified Assumptions: The theoretical model did not account for real-world complexities, such as shear flow distribution and warping.
Conclusion and Insights
This experiment demonstrated the challenges and value of identifying the shear center in structural design:
- Engineering Significance: Understanding the shear center is essential for minimizing torsion, reducing material usage, and enhancing safety in real-world applications.
- Cost Implications: Proper alignment with the shear center can prevent over-engineering and reduce costs associated with reinforcement and maintenance.
- Future Directions: Incorporating computational tools like ANSYS could refine this process, accounting for complexities overlooked in manual calculations.
Why It Matters
Understanding and applying the concept of the shear center transforms structures from merely functional to optimized. This experiment is a reminder that behind every stable bridge, secure building, or efficient aircraft, there is an engineer who took the time to find the balance.
Learn More
If you’re interested in diving deeper into this project, feel free to explore the following resources: