Strength Analysis of Wing Design with NACA 23012 Airfoil
Project Overview
Performed structural analysis on a wing design using the NACA 23012 airfoil to evaluate total deformation, maximum principal stress, and strain under operational loading conditions.
The importance of this project lies in ensuring the safety and reliability of aircraft under varying operational loads. By identifying areas of high stress and deformation, engineers can make informed design decisions to improve structural performance, enhance safety, and extend the lifespan of the wing. This analysis also helps optimize material usage, reducing weight while maintaining strength, which translates into cost savings and improved fuel efficiency for the aircraft. The results contribute to a better understanding of wing behavior under realistic conditions, paving the way for innovations in aeronautical engineering.
Problem Statement
Analyze the structural integrity of the wing by assessing deformation, principal stresses, and strain to ensure safety under operational loads.
Methodology
- Designed the wing structure using SolidWorks based on the NACA 23012 airfoil.
- Created a mesh with 0.1-meter elements in ANSYS for a detailed analysis.
- Applied lift forces and engine thrust to simulate real-world operational conditions.
- Used materials like aluminum alloy, carbon fiber, and PVC foam to balance strength and weight.
Analysis and Results
- Maximum deformation observed at the wingtip: 0.10467 meters.
- Peak principal stress: 1.8142e8 Pa on structural steel, within the material yield limit.
- Maximum principal strain: 0.002862 m/m, concentrated near the fuselage and leading edge.
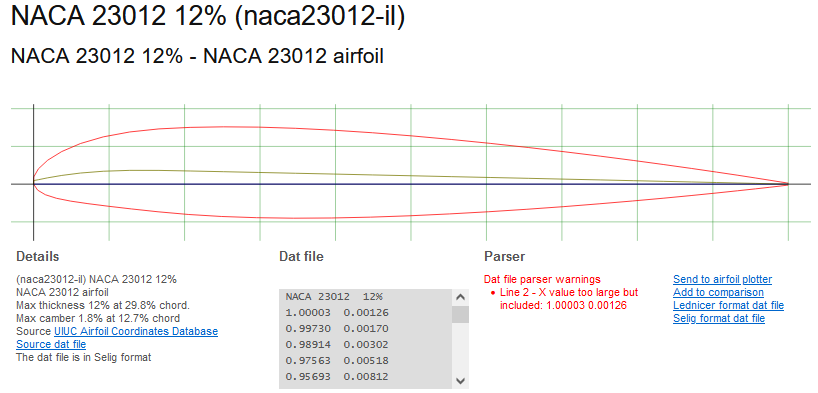
Figure 1: NACA 23012 Airfoil
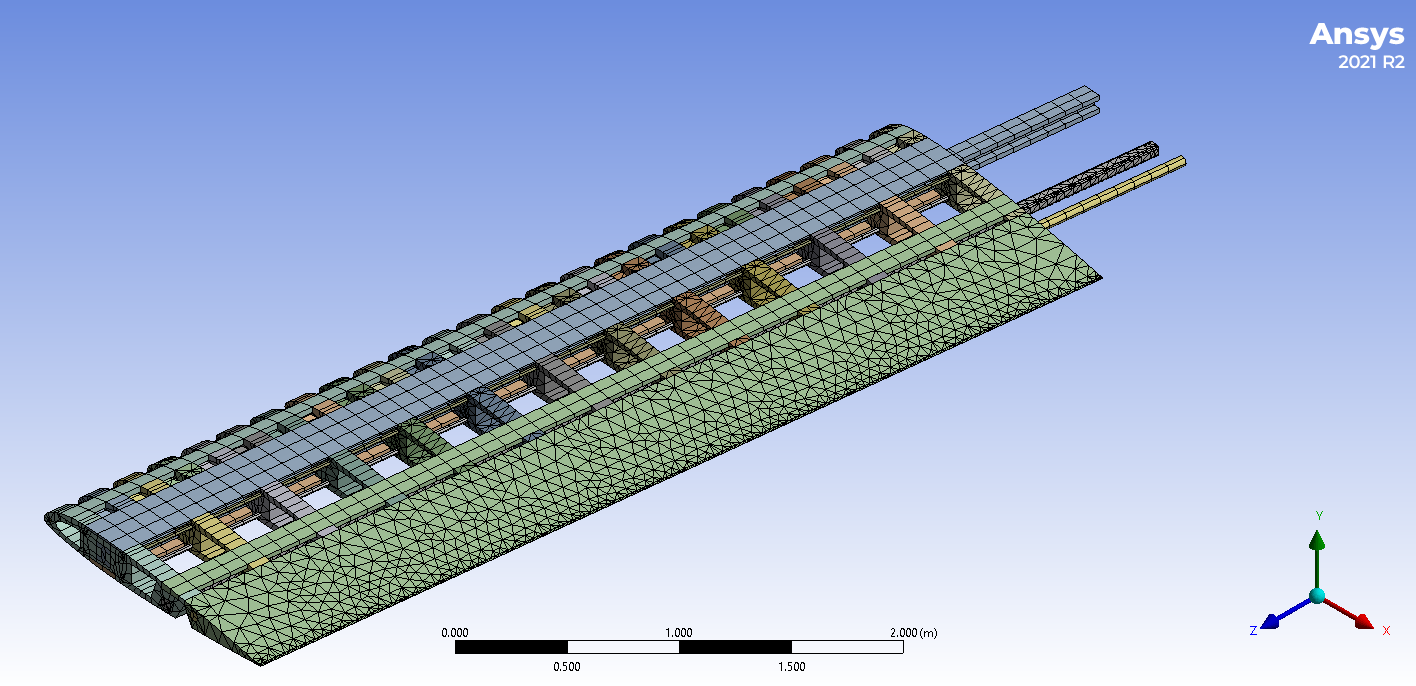
Figure 2: Mesh of the Wing Structure
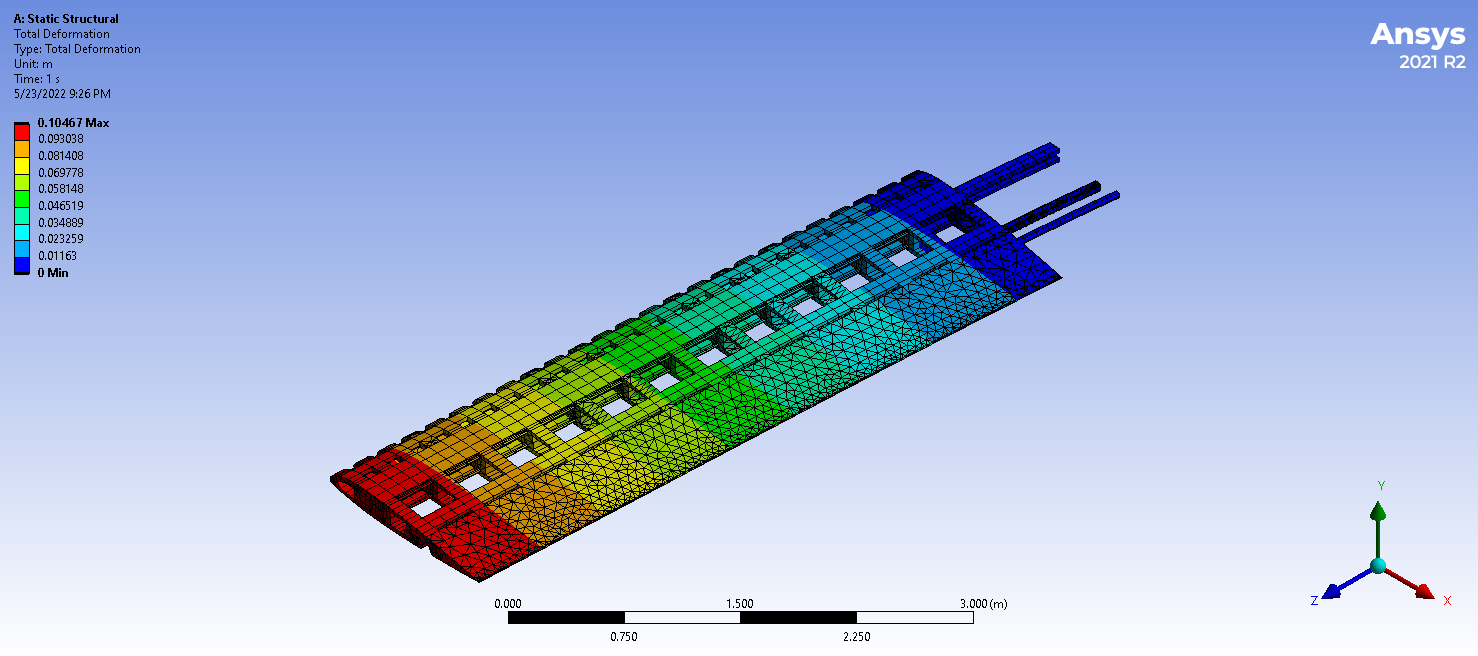
Figure 3: Maximum Deformation at the Wingtip
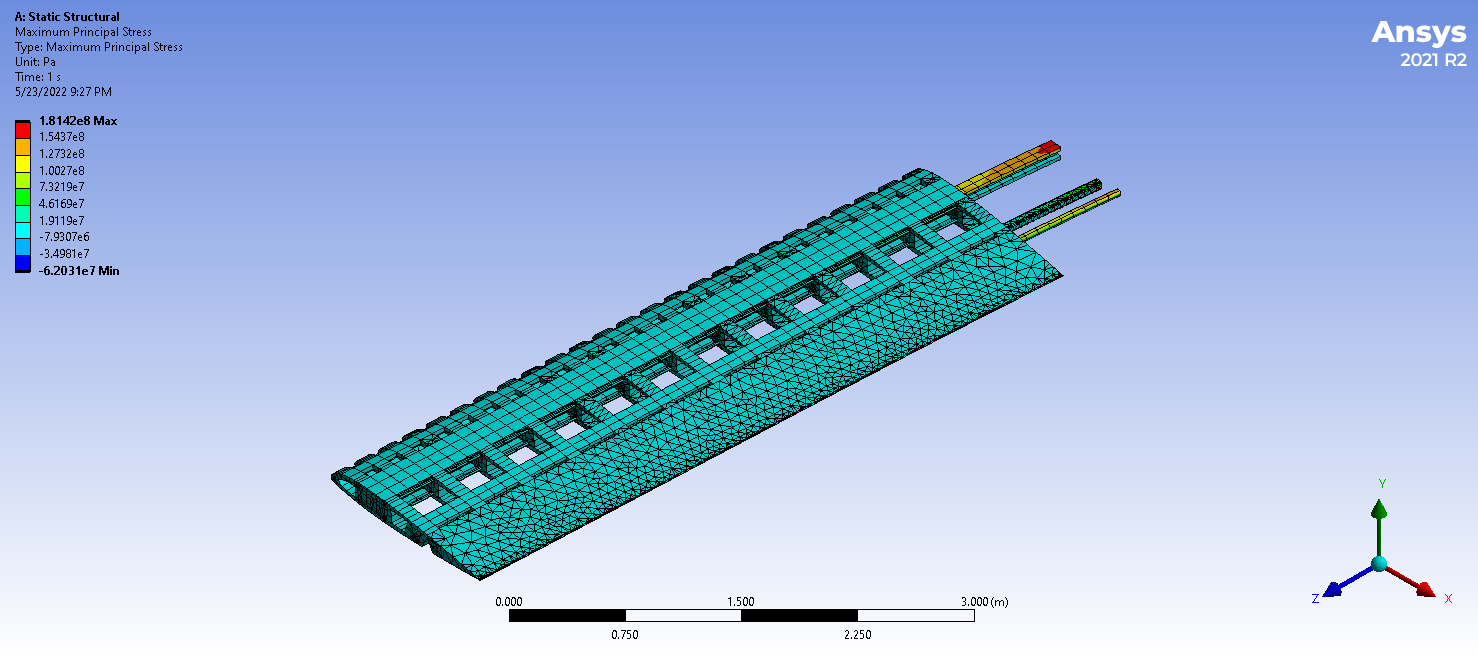
Figure 4: Principal Stress Distribution
Conclusion
The analysis validated the structural integrity of the wing under applied loads. The results confirmed that deformation, stress, and strain levels remain within safe margins, ensuring operational safety.
Tools and Skills Used
- ANSYS for Finite Element Analysis
- SolidWorks for 3D Modeling
- Stress, Strain, and Deformation Analysis
- Material Selection and Optimization
Learn More
If you’re interested in diving deeper into this project, feel free to explore the following resources: